STAGE I – MATERIAL SELECTION
Based on the information collected from the customer, we define the boundary work conditions of a given plastic element and then select the material that meets the requirements of the application. The mechanical properties and aesthetic values of a given product are assessed. For a typical injection molding application, the following aspects should be considered:
- element life cycle
- cooperation with other elements
- surface and color
- type and strength of the load
- intensity of use
- contact with chemicals
- impact strength
- air humidity
- exposure to UV rays
- ambient temperature
The analysis must guarantee the correct operation of the injected element at the lowest possible cost of material purchase. Working with reputable recyclers of plastics, we can also offer production from regrinds and regranulates from quality-controlled substitutes for original materials, while maintaining an appropriate quality regime.
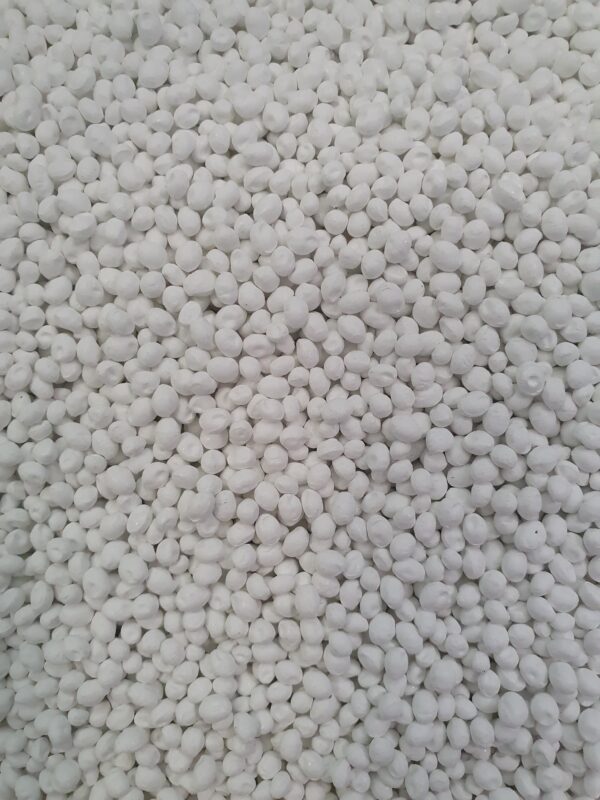
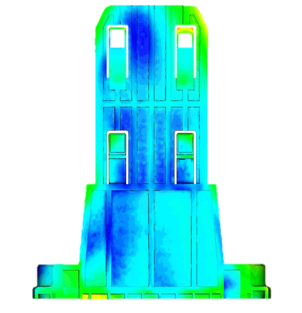
STAGE II – PART GEOMETRY OPTIMIZATION
With the mechanical and aesthetic requirements in mind, we begin the design phase of the molded part, which takes into account the requirements of the previously selected material. While designing a part, we optimize its wall thicknesses, add appropriate reinforcing ribs and eliminate hot spots. At this stage, strength calculations and simulations are also carried out in order to ensure the highest possible quality at the lowest possible production costs. Product weight optimization is one of the key design optimization elements.
The optimization of part geometry is carried out in terms of its technological nature in relation to the injection process, taking into account parameters such as parting lines, draft angles, venting and costs of the actual injection tool.
It should be remembered that even the best selected material will not ensure success if it is not followed by the proper element design.
STAGE III – INJECTION MOLD DESIGN
The mold design process is supported by the injection process simulation in order to fully optimize the mold cavity and the cooling system. Correct validation of the proposed design ensures the selection of optimal solutions for a given project. The scope of work at this stage can be divided into two areas:
Injection process simulation:
- selection of the optimal cooling system and materials for the injection mold in order to produce in the shortest possible cycle time with the highest quality
- selecting the optimal injection point location
- selecting optimal parameters of the injection process
- validation of part deformations and dimensional tolerance for a given product
- selecting appropriate sections of cooling channels
- optimization of the flow of the front of the material
Mold designer task:
- correct venting of the mold cavity and injection points
- selecting the optimal parting line for the part and mold
- selecting the appropriate kinematics for releasing a part from both the core and the cavity
- design of the optimal cooling system
- design of the mold with a specific injection molding machine in mind
- ensuring the appropriate stiffness of the mold
- ensuring the proper performance of the mold in terms of CNC machining and locksmith works
- optimal selection of gating and sprues
- creating 2D and 3D documentation
STAGE IV – INJECTION PROCESS OPTIMIZATION
Thanks to our proprietary seven-step mold optimization procedure, we are able to carry out a complete phase of testing and approval of any given mold. The customer receives full information on the technical condition of the mold and the necessary changes and corrections. Ultimately, the client acquires the optimal processing parameters for a given project. At this stage, if necessary, we also use the injection simulation, which enhances process optimization. We determine Cp and Cpk and characterize the deviations in which the injection mold works with the assumed injection parameters.
The cycle time requires meticulous analysis and verification of the process window for a given mold. Each new plastic injection molding project has three inherent goals: performance for the customer; production efficiency for the manufacturer; and reliability for the end user. DoE is the only way to finally verify the process capability and find the most efficient process that guarantees stable quality. The Design of Experiment methodology is one aspect of high precision injection molding that improves production efficiency both in terms of process stability and economic aspect. Working on the basis of DoE is the key to making right decisions because it reflects the essence of the entire process.
The main aim of this stage:
- Assessment of the process in terms of quality and capacity
- Finding optimal process parameters
- Assessment of the mold condition and its adjustments to optimize production
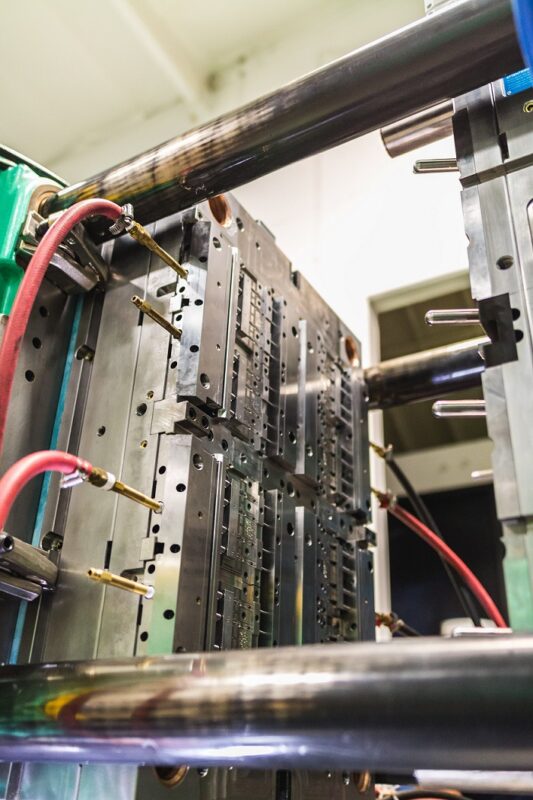
At the end of this stage, the customer becomes the owner of the described technological process, and his mold works in the shortest possible cycle time, in a stable manner that guarantees the appropriate quality of the final product.
In the case of existing projects, we offer injection mold validation, process capability assessment and then taking corrective actions to improve the production of a given element. We will help you answer the question whether the currently implemented production takes place with optimal process parameters, we will introduce adjustments and present recommendations that will allow you to generate savings while maintaining appropriate quality. The optimization process consists of:
Project audit – verification of production documentation and documentation of the injection mold. Assessment of documentation in terms of event registration, inspection planning, identification of production batches, supervision of the technological process.
Assessment of the part & mold design – Verification of tool technical condition and assessment of its design in terms of production efficiency. At this stage, we also use injection process simulations in order to find possible weaknesses and strengths of a given design.
Assessment of technical condition of aninjection molding machine on which the production order for a given element is carried out. The purpose of the verification is to check whether the machine is able to guarantee a stable, repeatable process.
Assessment of production parameters + process optimization in order to obtain the shortest possible time of the production cycle, which at the same time guarantees the highest process stability. The assessment is comprehensive and ends with the development of a technological process with a list of suggested corrective actions and mold modifications in order to generate further economic benefits.
After making corrections to the tool, we conduct further tests in order to obtain the most effective manufacturing process possible.
Assessment of control procedures: verification of implemented systems and quality levels together with the assessment of procedures and their suitability to protect against non-conforming products. The evaluation ends with a list of recommendations regarding modification of the control process or the development of completely new control procedures.
We also offer services in the field of analyzing the causes of complaints and finding the source of the problem in order to protect against the occurence of another non-compliance.
We offer validation of current suppliers and help in the selection of partners who are able to meet the technological and quality requirements of a customer. The following areas of activity are assessed:
- organization of products and materials identification
- functioning of the quality control department
- raw materials purchase policy
- repeatability of the production processes of given elements and cycle times validation
- assessment of procedures, corrective actions, preventive actions and potential problems risk assessment
- method of carrying out inspections of machines and injection molds
- assessment of the technical condition of selected customer injection molds
- assessment of infrastructure in terms of production planning and timeliness of orders
- assessment of the technical condition of the plastic preparation department
Unlike an ISO audit, the assessment focuses mainly on technical aspects that have a key impact on the quality of production. Today’s ISO audits focus mainly on the flow of documentation, as auditors usually do not have technical knowledge to effectively verify production nuances.
After the audit, a client receives a full report with both procedural and technical assessment of the company together with risk assessment of complaints or the lack of timely production. The audit can be carried out both for the purposes of assessing the manufacturer and verifying the occurrence of a complaint.